In the realm of field service management, particularly in industries like refrigeration, electrical networks, and logistics, a well-organized maintenance schedule is the linchpin for ensuring customer satisfaction, operational efficiency, and technician effectiveness. But what exactly is a maintenance schedule, and how does it differ from a maintenance plan? In this article, we will delve into the intricacies of maintenance scheduling, its crucial role in the industry, and how CMMS (Computerized Maintenance Management System) software can revolutionize your field service management.
Defining a Maintenance Schedule
In its essence, a maintenance schedule is a precise and dynamic calendar that orchestrates when your technicians perform maintenance, repairs, and servicing on equipment and installations, be it for commercial clients or individuals. These schedules break down the tasks into periodicities, such as daily, weekly, monthly, or annually. In the world of field service management, it’s the backbone for keeping equipment and systems running optimally.
However, it’s crucial to differentiate between a maintenance schedule and a maintenance plan. While both are vital, a maintenance plan is essentially an instruction manual that provides comprehensive guidelines, safety regulations, recommended practices, and all the necessary resources for maintenance, repair, and equipment control. In contrast, the maintenance schedule is your day-to-day action plan, detailing who does what and when.
Why Establish a Maintenance Schedule?
A well-structured maintenance schedule offers an array of benefits, contributing to both your organization’s internal efficiency and your external customer satisfaction. Here’s why it’s crucial:
- Enhanced Internal Organization: Maintenance schedules empower your teams to proactively plan their workdays, making them more productive and better prepared for the tasks at hand.
- Improved Customer Satisfaction and Loyalty: For customers, reliability is paramount. Keeping your maintenance appointments as scheduled is a surefire way to maintain their trust and loyalty.
The Benefits of a Robust Maintenance Schedule
Creating and maintaining an effective maintenance schedule is not just about punctuality; it brings a host of advantages:
- Priority Management: Efficiently prioritize equipment and contracts based on their needs and deadlines.
- Extended Equipment Lifespan: Timely maintenance ensures your customer’s equipment lasts longer, saving them money and earning their trust.
- Balanced Workload: Evenly distribute tasks among your technicians, preventing overloading and ensuring efficient use of resources.
- Improved Task Management: Stay on top of your maintenance activities, avoiding oversights or unnecessary delays.
- Optimized Routes: Minimize travel time, increase the number of interventions, and ultimately reduce costs.
- Time Savings: Efficient planning saves time, making your operations smoother and more cost-effective.
- Customer Satisfaction: A well-maintained schedule guarantees that customers’ expectations are met and exceeded.
- Satisfied Technicians: Your technicians benefit from a more predictable and less stressful work environment.
Establishing an Effective Maintenance Schedule
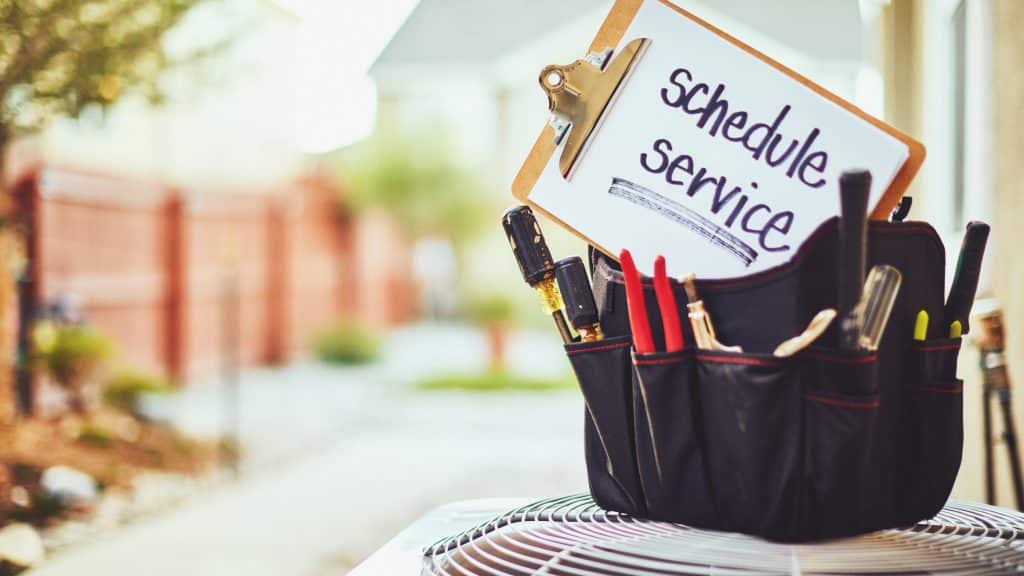
Building a maintenance schedule that works for your field service management requires careful planning. Here’s how you can create one:
- Determine Recurrence: Begin by identifying all the maintenance tasks, specifying their frequencies, and associating them with the relevant technicians. Whether it’s daily, weekly, or annual, knowing how often each task needs to be performed is crucial.
- Maintain a Safety Margin: In the world of field service management, surprises are common. To accommodate unexpected incidents, always leave a margin for unforeseen circumstances in your schedule.
- Prioritize and Plan for Emergencies: When emergencies arise, prioritize them based on their urgency. This entails assessing the problem, ordering any necessary parts, and communicating the details to the technicians responsible for the task.
- Produce Comprehensive Reports: After each maintenance operation, it’s vital to have your technicians create detailed maintenance reports. These reports include what was done, which parts were replaced, and the time taken. They serve as invaluable records for future maintenance.
Leveraging Tools for Effective Maintenance Scheduling
While Excel is often the default choice for creating schedules, there are more sophisticated and efficient tools available, such as CMMS software. CMMS integrates maintenance scheduling into its functionalities, making the process significantly more streamlined.
With CMMS, programming intervention recurrence, associating technicians, and accessing maintenance reports become a breeze. The software enables real-time scheduling modifications, sending notifications directly to your technicians. This not only ensures they are informed but also offers them the flexibility to adapt to any changes.
Beyond scheduling, CMMS simplifies record-keeping, allowing you to generate quotes, invoices, contracts, and electronic signatures with ease. Post-intervention notices are automatically sent to your customers, further improving customer satisfaction and loyalty.
In conclusion, a meticulously planned maintenance schedule is the cornerstone of exceptional field service management. By embracing modern solutions like CMMS software, you can elevate your maintenance scheduling, leading to better operational efficiency, increased customer satisfaction, and a more streamlined workflow. Don’t wait; request a free demo and revolutionize your field service management today!